Manufacturing Process
Pultrusion Overview
Pultrusion is the process of “pulling” raw
materials - glass and resin - through a heated die creating a continuous composite profile. Wagners uses the ‘Pultrusion Process’ to manufacture structural Fiber Reinforced Polymer (FRP) sections.
These sections are similar in geometry and shape to traditional cold-formed steel ‘RHS’ sections but are made from glass fibers and vinyl ester resins. The diagram demonstrates the process from start to finish
Benefits of our Pultruded structural profiles include:
- Lightweight - 20% the weight of steel, 40% that of treated timber
- Extremely high strength to weight ratio
- Chemically inert
- Environmentally stable, extremely low coefficient of thermal expansion
- Does not rust or rot
- Non-conductive
- Quick and easy installation
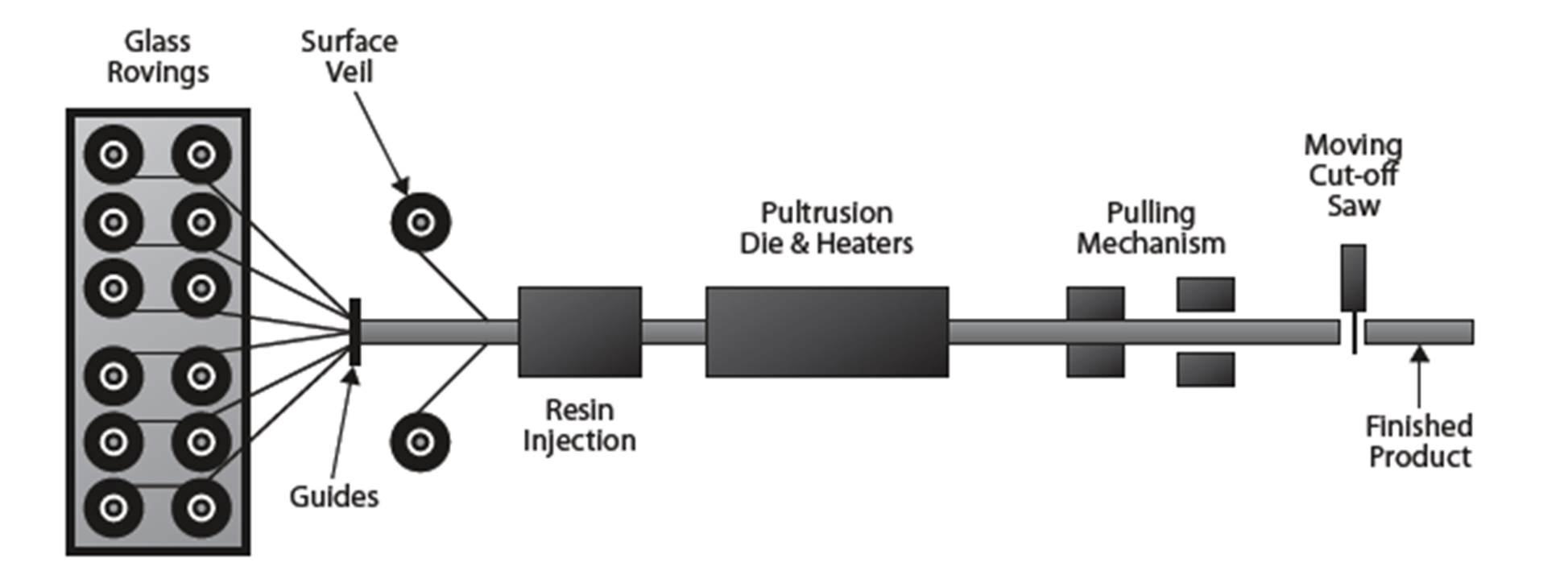
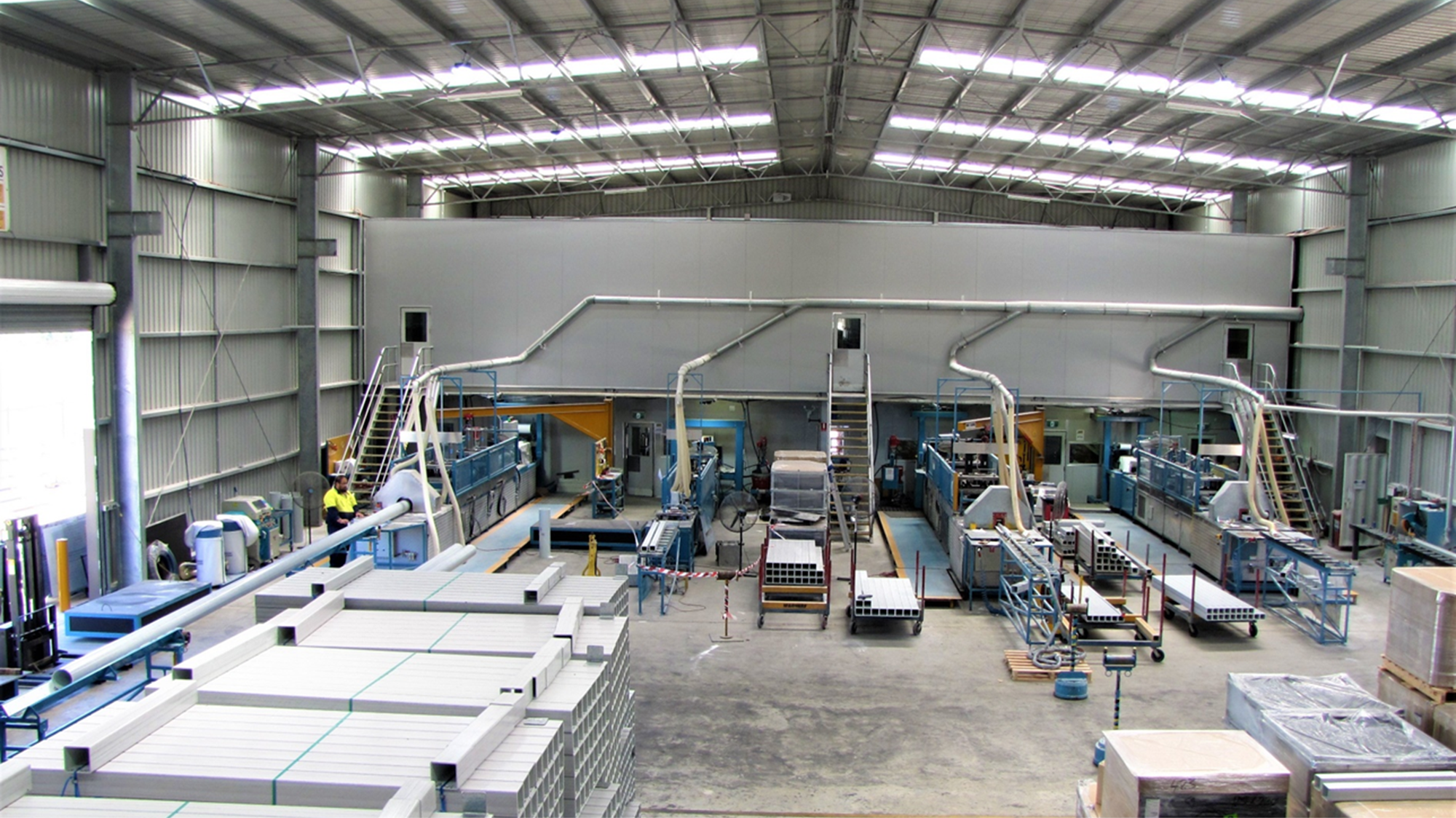
A Deeper Look into the Pultrusion Process
The term pultrusion combines the words, “pull” and “extrusion”. Extrusion is the
pushing of material, such as a billet of aluminum, through a shaped die, whereas
pultrusion, is the pulling of material, such as fiber and resin, through a shaped die.
The pultrusion process starts with racks holding rolls of fiber roving (thread). The
fiber reinforcement used by Wagners CFT is glass fiber. This raw fiber is pulled off the
racks and is guided to the necessary shape, orientation and layers before entering
a resin injection system. A surface veil is incorporated to improve surface finish and
provide resistance to UV degradation.
The fiber reinforcement becomes fully injected (wetted-out) with the catalyzed resin
such that all the fiber filaments are thoroughly saturated with the resin mixture. This
wetted fiber then enters the heated curing die. The heat initiates a chemical reaction
in the resin which causes it to harden, and the finished profile exits the die and is
subsequently cooled. The movement for the process is created by puller clamps
which act on the finished product and pull it on a continuous basis.
At the end of this pultrusion machine is a moving cut-off saw. The pultruded profiles
are cut to the specific length and stacked.